Chemical Exposure Monitoring (CEM) at the Workplace
Chemical exposure monitoring involves assessing the level of workers’ exposure to hazardous chemicals and evaluating the adequacy of existing control measures. Workers’ exposure to these chemicals through inhalation can be measured by conducting air monitoring.
Air monitoring is the process of quantifying or determining the identity of a chemical using standard sampling instruments, techniques, and strategies. A sampling device is employed to separate and collect the contaminant from a measured volume of the atmosphere.
The contaminant can be quantified instantaneously using direct reading instruments. Integrated air sampling instruments can be used to measure airborne hazardous chemicals according to validated methods. The chemical levels in the atmosphere are then established in terms of mass or number concentration for particulates, or volume concentration for gases and vapors.
What is Chemical Exposure Monitoring (CEM)?
Chemical exposure monitoring is a critical aspect of workplace safety, governed by the Occupational Safety and Health (Use and Standard of Exposure of Chemicals Hazardous to Health) Regulations 2000 (USECHH Regulations). These regulations define Chemicals Hazardous to Health (CHTH) as any chemical or preparation that is:
- Listed in Schedule I or II of the USECHH Regulations;
- Classified under any hazard class specified in the Health Hazards of the First Schedule of the Occupational Safety and Health (Classification, Labelling and Safety Data Sheet of Hazardous Chemicals) Regulations 2013 [P.U.(A) 310/2013] or as amended;
- Defined as a pesticide under the Pesticides Act 1974 [Act 149] or as amended; or
- Listed in the First Schedule of the Environmental Quality (Scheduled Wastes) Regulations 2005 [P.U. (A) 294/2005] or as amended.
The USECHH Regulations mandate that employers conduct a chemical health risk assessment (CHRA) for each work activity involving the use and exposure of CHTH to workers. This assessment must be carried out by an assessor who is appointed by the employer and registered with the Department of Occupational Safety and Health (DOSH).
One of the key responsibilities of the assessor is to determine the necessity of chemical exposure monitoring for each assessed work unit. Chemical exposure monitoring must be conducted under the USECHH Regulations when an assessment of health risk indicates that:
- Monitoring is required to ensure workers’ exposure does not exceed the Permissible Exposure Limit (PEL) or is maintained at the lowest practicable level; or
- Monitoring is necessary to ensure the adequacy of control measures for worker exposure to CHTH.
The PELs for CHTH are specified in Schedule I of the USECHH Regulations.
Purposes of Chemical Exposure Monitoring (CEM)
Generally, the purposes of air monitoring conducted at the workplace include:
- To help towards the design of exposure control measures and to evaluate the effectiveness of control measures;
- Evaluation of exposure level relative to an exposure limit;
- As periodic monitoring to meet regulatory requirements;
- Measurement of initial or baseline exposure data;
- Providing a historical record of worker’s exposures for company and worker’s records;
- Identification of potential overexposure situations or high-exposure activities; and
- Identification of contaminants in an emergency situation (such as a hazardous chemical spill), or in an unknown atmosphere (as in a confined space).
How is Chemical Exposure Monitoring (CEM) Conducted?
The monitoring is conducted in accordance with the principles outlined in the guidelines established by the Department of Occupational Safety and Health (DOSH), specifically the “Guidelines on Monitoring of Airborne Chemical Hazardous to Health 2022.”
Below are the steps or methodologies taken during the monitoring.
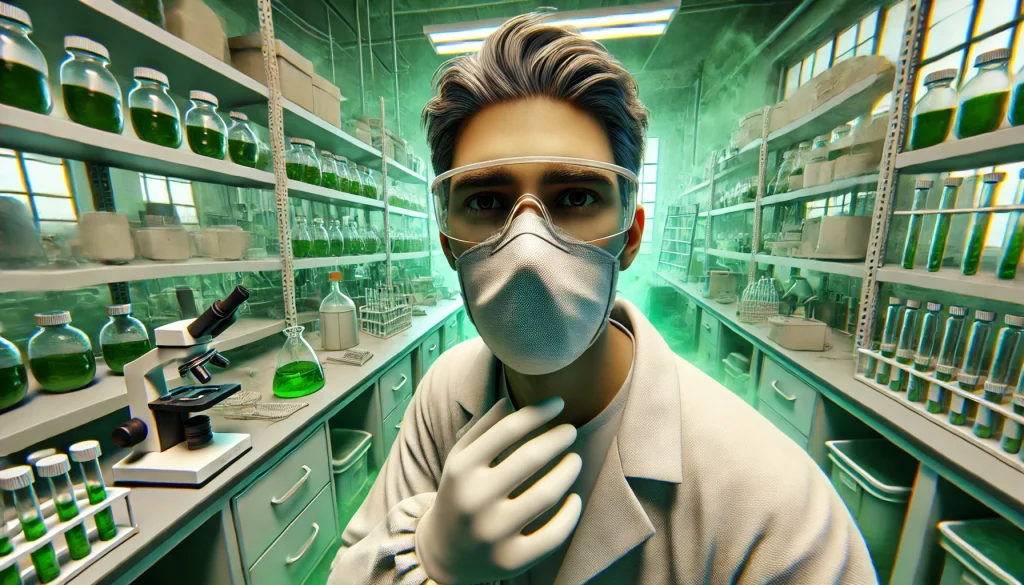
What are Included in the CEM Report?
The chemical exposure monitoring (CEM) report will be divided into several main sections, each containing core elements essential to the monitoring as per outlined by Chapter 7 – Report Writing of the guidelines. While the layout of the report may vary slightly between consultants and practitioners, this variation can be attributed to factors such as personal preferences, industry-specific best practices, and client requirements.
The core sections of the report are as follows:
Benefits of CEM to the Organization
Generally, conducting chemical exposure monitoring (CEM) of chemicals hazardous to health (CHTH) at the workplace offers several important benefits to your organization such as:
1. Protection of Worker Health
Chemical exposure monitoring helps identify hazardous chemicals in the workplace, allowing employers to take appropriate measures to mitigate risks. By monitoring exposure levels, employers can prevent adverse health effects such as respiratory problems, skin irritations, and long-term illnesses related to chemical exposure. Consequently, the monitoring enables the early detection of overexposure to harmful chemicals, allowing for timely intervention and reduction of health risks.
2. Compliance with Regulations
Chemical exposure monitoring also ensures compliance with Occupational Safety and Health (Use and Standards of Exposure of Chemicals Hazardous to Health) Regulations 2000 (USECHH Regulations) and other relevant legal requirements. Most importantly, regular monitoring helps employers avoid penalties and legal liabilities associated with non-compliance.
3. Improved Workplace Safety
Chemical exposure monitoring provides data for conducting health risk assessments, helping to identify high-risk areas and processes. Furthermore, the monitoring serves as vital opportunity for your organization to evaluate the effectiveness of existing control measures, such as ventilation systems and personal protective equipment (PPE), leading to improvements in workplace safety.
4. Informed Decision-Making
Chemical exposure monitoring provides accurate data on chemical exposure levels, enabling informed decision-making regarding safety protocols and control measures. Employers can use monitoring data to continuously improve workplace safety practices and reduce exposure risks.
5. Protection of Company Reputation
By conducting regular chemical exposure monitoring, companies demonstrate their commitment to employee safety and health, enhancing their reputation. A safe work environment builds trust with employees, customers, and stakeholders, leading to improved employee morale and business relationships.
6. Historical Exposure Records
Chemical exposure monitoring provides a historical record of workers’ exposure levels, which can be valuable for future reference and health assessments. In case of health claims or investigations, historical data can support the evaluation of exposure-related issues and protect your organization from false workers’ claim.
7. Optimization of Resources
Lastly, chemical exposure monitoring helps prioritize areas requiring intervention, ensuring that resources are allocated effectively to manage exposure risks. By identifying and mitigating risks early, companies can reduce costs associated with health care, absenteeism, and regulatory fines.
Chemical Exposure Monitoring (CEM) FAQs
References
- Occupational Safety and Health Act (OSHA) 1994.
- Occupational Safety and Health (Use and Standards of Exposure of Chemicals Hazardous to Health) Regulations, 2000.
- Guidelines on Monitoring of Airborne Chemical Hazardous to Health 2022.